Performance and Profit: Small Repairs, Big Impact
How repair segmentation can lead to major gains in efficiency and profit.
Whether there are external pressures or not, improved operational efficiency is beneficial to all stakeholders. It benefits the customer through a more timely repair, the insurer through reduced claim costs and, perhaps most importantly, the repairer through improved profitability.
Let’s examine a key area of potential efficiency gains: repair efficiency by repair segment (total RO hours). We’ll break the repair segments into four categories and compare the performance of two similar shops.
- X Press = < 10 Hours
- Light = 10 – 20 Hours
- Medium = 20 – 40 Hours
- Heavy = 40 + Hours
As illustrated below, the touch times and resulting cycle times for the X Press and Light segments have a negative impact on Shop #1’s performance.
There is a real opportunity to improve performance in these two repair segments, where complexity of the repair and parts-related issues are less of a constraint.
Shop # 1
X Press and Light repairs make up at least 50% of the average shop’s repair count.
What would be the impact of the average shop improving its performance in these segments?
By comparison, there is a significant difference in Shop # 2’s repair efficiency by segment (shown below).
Which illustration is more representative of your shop? Hint: 80% of the industry is performing at levels similar to Shop # 1.
Shop # 2
What is the impact of overall Cycle Time and Touch Time for these shop comparisons? As shown in the tables below, Shop # 2 repairs vehicles twice as fast as Shop # 1.
Shop # 1
Shop # 2
Performance = Profit
Shop #2 delivers more repairs per month. Those repairs are generating more gross profit per month with very little increase in the shop’s monthly fixed operating costs. The result is higher net profit.
The common thread in our analysis of high performing repairers is that they have a best practice in place for smaller repair segments. In most cases this involves an immediate chain of events that is triggered by “keys in”. There is a structured communication flow between departments, and this results in a technician beginning their “touch time” of the vehicle within an hour of arrival.
If you’re currently treating all repairs as equals, you may want to consider a change. Using repair size to determine scheduling or work improves efficiency and lowers costs and that benefits all stakeholders.
Discover how Terminal Auto Body transformed their business by embracing a data-driven mindset. Learn how they improved financials, reduced WIP, and achieved operational excellence.
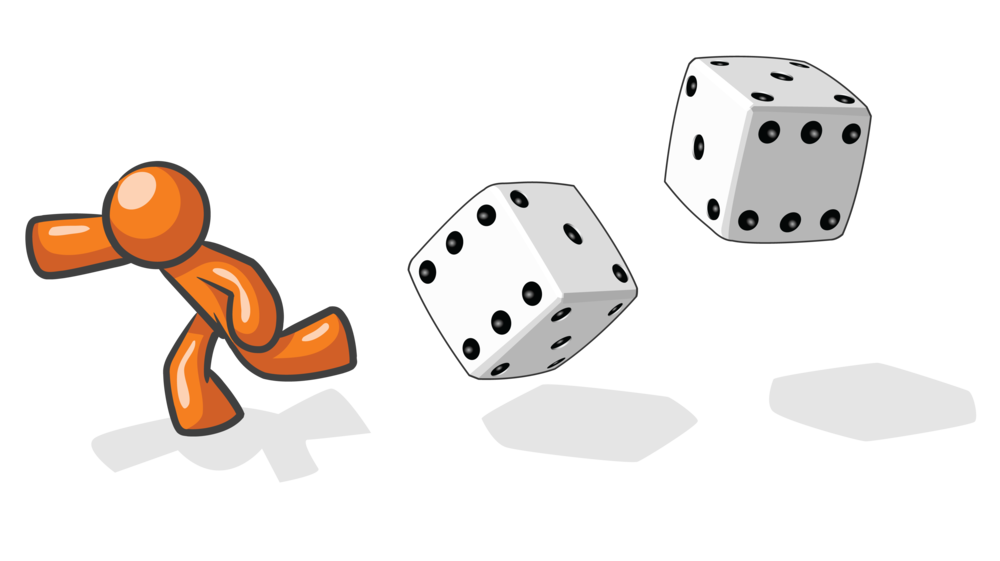